Revolutionizing Manufacturing with Production CNC Machining
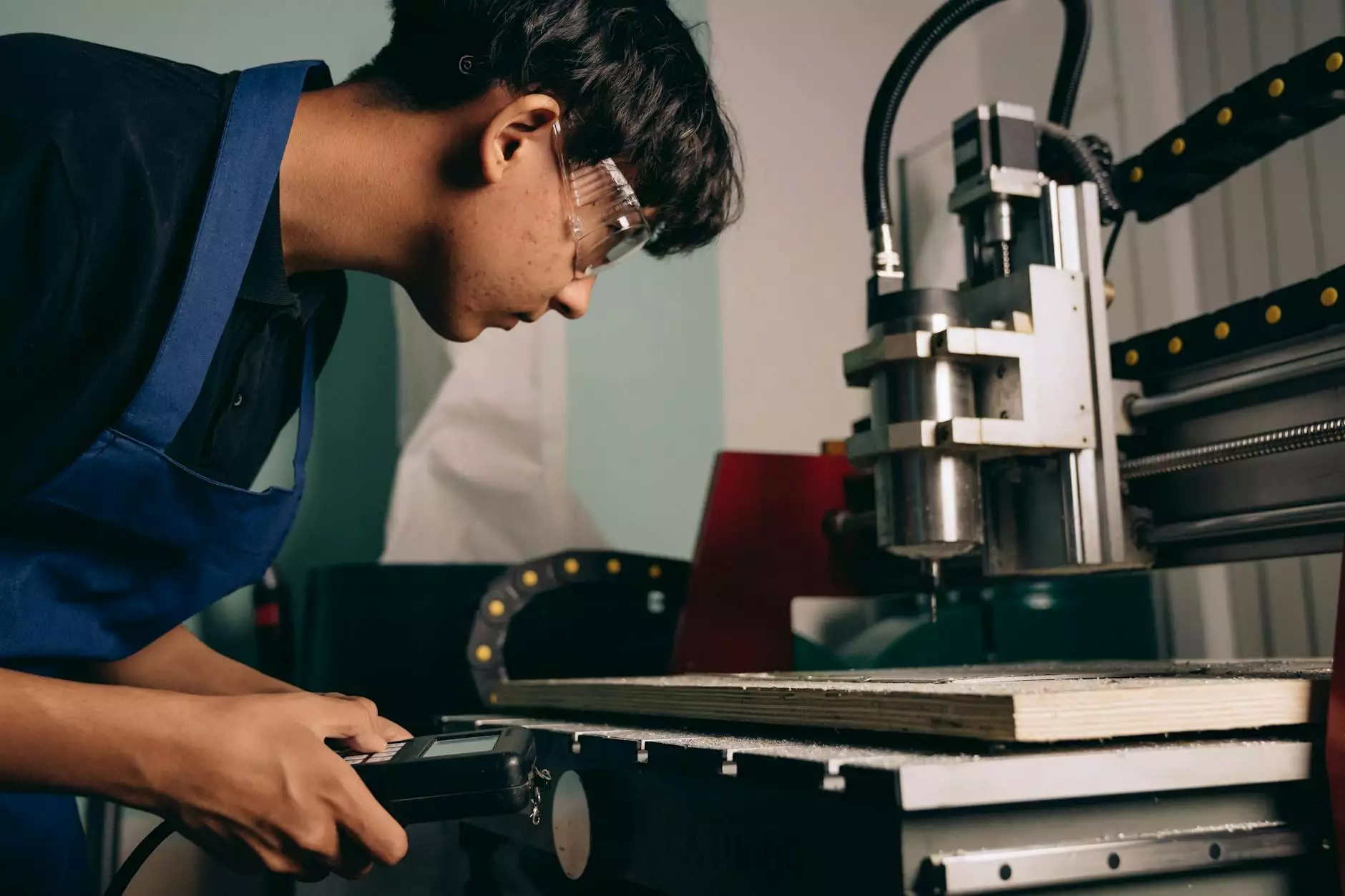
In the fast-paced world of manufacturing, production CNC machining has emerged as a cornerstone technology that is reshaping various industries. As businesses strive for greater efficiency, precision, and cost-effectiveness, CNC machining is at the forefront, providing unique solutions that enhance production rates and quality. This article delves into what production CNC machining is, its advantages, applications, and why it's essential for modern manufacturing.
Understanding Production CNC Machining
CNC machining, or Computer Numerical Control machining, is a manufacturing process where pre-programmed computer software dictates the movement of factory tools and machinery. From milling and turning to grinding, CNC machines can precisely control a wide range of complex tasks that were once performed manually. This technology is instrumental in production CNC machining, which focuses on the large-scale production of parts and components that meet stringent specifications.
The Process of CNC Machining
The CNC machining process involves several critical steps:
- Design: The first step is creating a detailed design using CAD (Computer-Aided Design) software, which translates the design into a geometrically defined model.
- Programming: The CAD file is then converted into CNC code, or G-code, a language that tells the CNC machine how to move and operate.
- Setup: The CNC machine is set up with the necessary tools and materials. This includes securing the workpiece on the machine.
- Machining: Once programmed and set up, the CNC machine starts to execute the machining process, performing tasks such as cutting, drilling, and milling.
- Quality Control: Throughout the process, quality checks are conducted to ensure that the final products adhere to the required specifications.
The Advantages of Production CNC Machining
Production CNC machining is synonymous with numerous advantages that make it a preferred choice for manufacturers:
- Precision: CNC machines are capable of achieving tolerances as tight as 0.001 inches, making them ideal for applications where precision is paramount.
- Consistency: Once programmed, CNC machines replicate the same process over and over, providing consistency in production quality.
- Speed: CNC machining reduces production time significantly, enabling manufacturers to meet tight deadlines without compromising quality.
- Flexibility: The quick change of CNC programs allows manufacturers to switch between different designs or product lines with ease, accommodating changing market demands.
- Reduction in Waste: The precision of CNC machining leads to a decrease in material waste, as parts are cut more accurately and efficiently.
Applications of Production CNC Machining
Production CNC machining is utilized across a spectrum of industries, demonstrating its versatility and adaptability. Some key applications include:
- Aerospace: In the aerospace industry, CNC machining is used to create intricate parts such as brackets, housings, and turbine engine components that require high precision and reliability.
- Automotive: It plays a crucial role in the automotive sector for manufacturing parts, including engine components, transmission parts, and custom tooling.
- Medical Devices: The medical field often requires CNC-machined components, such as surgical instruments and implants, that must meet stringent regulatory standards.
- Electronics: CNC machining is essential in the production of casings and enclosures for electronic devices, providing the precision necessary for complex assembly.
- General Manufacturing: Beyond specialized industries, CNC machining is a standard process in general manufacturing, producing everything from custom machinery to consumer goods.
Innovative Practices in Production CNC Machining
As technology advances, so does the field of production CNC machining. Innovative practices that enhance efficiency and production capabilities continue to emerge:
Integration of Automation and Robotics
One of the most significant advancements in CNC machining is the integration of automation and robotics. Automated CNC machines can operate continuously, minimizing manual intervention and further increasing production efficiency. Robotics can be employed for loading and unloading materials, allowing for a fully automated production line.
IoT and Smart Manufacturing
The rise of the Internet of Things (IoT) has led to the advent of smart manufacturing. Machines equipped with sensors collect data in real-time, allowing manufacturers to monitor performance, detect anomalies, and optimize machining processes remotely. This data can be analyzed to improve future production runs, leading to better quality and efficiency.
Advanced Materials
Production CNC machining is also adapting to use advanced materials such as composites, titanium, and high-strength alloys. These materials, while often more challenging to work with than traditional metals, provide enhanced properties that are beneficial in many applications, particularly in aerospace and automotive sectors.
Choosing the Right CNC Machining Partner
Finding the right partner for production CNC machining is critical for manufacturers looking to streamline their operations and enhance product quality. Here are some factors to consider:
- Experience and Expertise: Ensure that the CNC machining service provider has significant experience in your industry and the specific requirements needed for your components.
- Capabilities: Evaluate the facilities and technologies of the provider. They should have advanced CNC machinery and the ability to work with various materials.
- Quality Assurance: A commitment to quality control and adherence to industry standards is essential. Look for certifications such as ISO 9001.
- Customer Support: Effective communication and support during the design and production process can make a significant difference in service quality.
- Turnaround Time: Assess the company’s ability to meet your timelines without sacrificing quality.
The Future of Production CNC Machining
The future of production CNC machining is bright, with continued advancements expected in technology, materials, and processes. Manufacturers are likely to see:
- Higher Levels of Customization: As customer demands evolve, CNC machining will increasingly support personalized and specialized products.
- Increased Efficiency: Continued improvements in software and hardware will further streamline CNC machining processes, reducing production times and costs.
- Sustainability Practices: As the manufacturing industry moves towards more sustainable practices, CNC machining will incorporate eco-friendly methods and materials, reducing environmental impact.
- Integration of AI: Artificial Intelligence (AI) will play a more prominent role in optimizing machining operations, predicting maintenance needs, and enhancing decision-making processes.
Conclusion
In conclusion, production CNC machining is revolutionizing the manufacturing landscape by offering precision, efficiency, and adaptability. Whether in aerospace, automotive, or other industries, CNC machining stands as a testament to the innovations that enhance production capabilities. As technology continues to advance, businesses that embrace these strategies will undoubtedly remain at the forefront of their industries, achieving unmatched quality and efficiency in their operations.
Final Thoughts
If you are looking to improve your manufacturing processes, partnering with a professional CNC machining service like DeepMould.net can offer you the edge needed in today's competitive environment. Embrace the future of manufacturing with production CNC machining and watch your business flourish!