Understanding Metal Die Casting Manufacturers
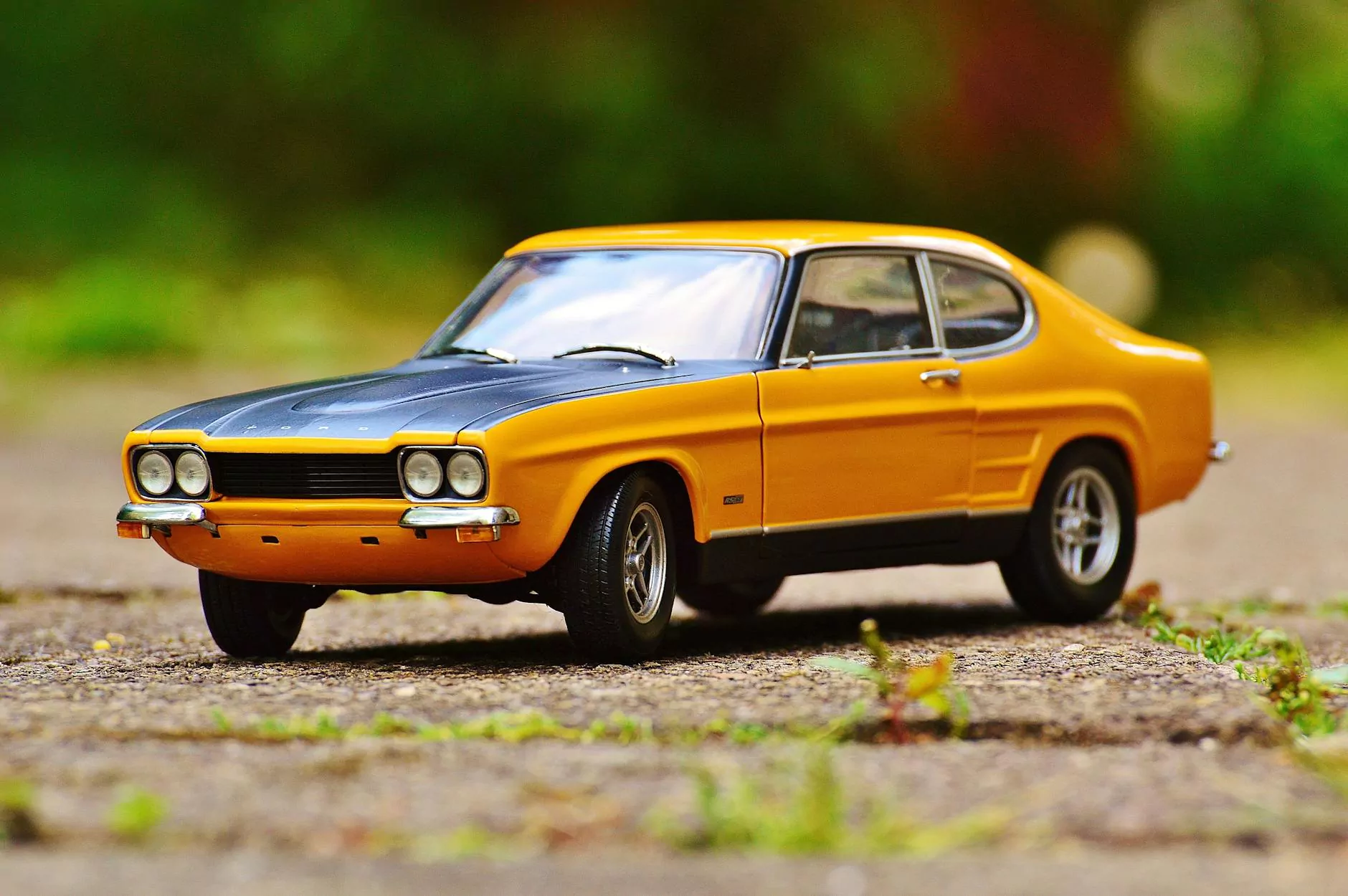
Metal die casting manufacturers play a pivotal role in various industries, providing the foundation for creating components that are essential to modern machinery, electronics, automotive parts, and much more. This article delves into the intricate world of die casting, offering insights that will benefit anyone seeking knowledge about this critical manufacturing process.
What is Metal Die Casting?
Metal die casting is a process that involves forcing molten metal into a mold to create a desired shape. It is a highly efficient manufacturing technique that produces parts with incredible precision and a high-quality finish. This method is widely employed across different sectors due to its ability to create complex geometries and maintain tight tolerances.
The Die Casting Process
The die casting process can be broken down into several key steps:
- Mold Preparation: The die (mold) is created using high-quality steel or other metals, designed specifically for the shape of the desired part.
- Melting the Metal: The chosen metal alloy is melted in a furnace. Common materials include aluminum, zinc, and magnesium.
- Injecting the Metal: Molten metal is injected into the die under high pressure, ensuring that all cavities are filled.
- Cooling: The molten metal is allowed to cool and solidify within the die. This step is crucial for achieving the desired dimensions and strength.
- Removing the Cast: Once cooled, the die is opened, and the solidified part is ejected. Additional finishing processes may be employed at this stage.
Advantages of Metal Die Casting
There are several advantages to utilizing the services of metal die casting manufacturers:
- Precision: Die casting generates components with exceptional accuracy, which is essential for parts with intricate details.
- Strength: The die-cast parts offer superior strength compared to other manufacturing methods like plastic injection molding.
- Cost-Effectiveness: Once the die is created, the cost per unit decreases significantly with higher production volumes.
- Rapid Production: The process allows for fast production rates, making it ideal for large batch productions.
- Material Versatility: Various metal alloys can be used, providing manufacturers with flexibility depending on application requirements.
Applications of Metal Die Casting
Metal die casting finds applications across a multitude of industries:
Automotive Industry
The automotive industry is one of the biggest users of die casting. Parts such as engine blocks, transmission cases, and wheels are commonly produced using this method due to the strength and light weight of the components.
Aerospace Industry
In aerospace, strict weight and performance standards make die casting an attractive option. Components such as brackets and housings are crafted to meet the stringent criteria necessary for flight safety.
Electronics
Electronics manufacturers rely on die casting for casings and housings that require excellent thermal conductivity and durability. Aluminum die casting is particularly popular for electronic components due to its lightweight and versatile properties.
Choosing the Right Metal Die Casting Manufacturer
Selecting a competent manufacturer is crucial for obtaining high-quality die-cast components. Here are various factors to consider:
Experience and Expertise
The first aspect is to evaluate the manufacturer’s experience. A company with extensive experience in the field will possess the knowledge to manage complex projects efficiently.
Capabilities and Technologies
Look for manufacturers that employ modern technologies, such as computer-aided design (CAD) and advanced molding technologies, enabling the production of intricate designs accurately.
Materials Used
Different manufacturers may specialize in different materials. Ensure that they can handle the specific alloys you require for your components to guarantee compatibility with your products.
Quality Control Standards
Quality assurance is paramount in die casting. Verify that the manufacturer follows industry standards and implements rigorous testing protocols to ensure all products meet quality expectations.
Customer Support
A reliable manufacturer will offer excellent customer service, assisting you throughout the production process, from initial design consultations to final delivery.
The Future of Metal Die Casting
The future of metal die casting manufacturers looks promising, with several advancements on the horizon:
Automation and Smart Manufacturing
The integration of automation and IoT technologies is enabling manufacturers to increase efficiency and reduce human error. Automated processes will be able to monitor production in real-time, ensuring quality and consistency.
Alloy Development
New metal alloys are continuously being developed that enhance the performance characteristics of die-cast products. For instance, advancements in aluminum alloys are increasing the strength-to-weight ratio further, enhancing applications in industries like automotive and aerospace.
Sustainability in Manufacturing
Sustainability is becoming increasingly essential in manufacturing. Metal die casting is inherently more environmentally friendly compared to some other processes, but manufacturers are now focusing on recycling materials and reducing waste to meet environmental standards.
Conclusion
In conclusion, metal die casting manufacturers are essential players in today's manufacturing landscape, providing high-quality components for a wide range of applications. By understanding the nuances of the die casting process, its advantages, and the key factors to consider when choosing a manufacturer, businesses can leverage this valuable manufacturing technique to improve their products and their bottom line.
Whether you are in the automotive, aerospace, or electronics industry, collaborating with proficient die casting manufacturers like Deep Mould can significantly enhance your product's quality and performance. Take the time to explore your options, and invest in the future of your manufacturing needs.